About
I began working professionally as a mechanical engineer in 2002, when I graduated with my Mechanical Engineering degree (MS ’09). However, the conviction to pursue engineering started much earlier than college. Early in high school I realized I wanted to be an engineer. Fortunately, more than 25 years later I have never questioned that path.
My career has journeyed through defense, aerospace, and the consumer product industries. Along the way each employer, colleague, professor, and project has taught me a wide range of skills. I believe that I’ve also made an impression on them as well.
While I’m detail oriented—occasionally frustratingly so for some—I also have a big picture point of view. A myopic stance towards engineering likely will create other problems for the company. A holistic approach needs to be considered.
As the saying goes, “garbage in, garbage out,” a broken product development process can’t sustain successful, innovative, and well engineered products in the long term. Often, small shortcuts and sloppiness can happen without much impact to a product. Over time, however, these can metastasize into big problems that require considerable time and effort to correct—the most difficult being the culture that allowed them to happen in the first place. I endeavor to improve best practices and sound processes regardless of the organization’s size because in the long term it is more beneficial to everyone.
I think the following quote captures the healthy tension between processes, big picture view, and attention to detail.
It is healthy to have some degree of process intolerance—an innate disdain of undue procedures and waiting. After all, waiting for a green light never gets you there first; though red lights certainly prevent accidents.
Scott Belsky, The Messy Middle
An overarching professional goal lately has been my interest in contributing to industries that are committed to responsibly benefiting their customers, employees, environment, and their community. While some companies in consumer products and aerospace can and are executing on these ideals, more companies in the sustainable energy, green technology, and medical industries are leading the way. Hopefully this is a sentiment that quickly sweeps many aspects of our life and the companies that produce goods and services for society.
Skills
Modeling
Spanning +20 years, I’ve used most of the mainstream packages out there: Solidworks, NX, CATIA, Pro/E, etc. In aerospace the main challenge is large assemblies, often requiring kinematic control. Complex class A surface modeling in consumer products has been my most recent challenge, often in collaboration with an Industrial Designer. Regardless if the product is one part or thousands, building robust, flexible, and intuitive models is my goal.
Simulation and FEA
Pretty CAD models are great, but will they work? My FEA experience helps inform the design process whether the next step is a prototype or mass production. Simple linear static analysis is typically the first level. After that, increasing complexity and realism with contact and nonlinear material properties. Fatigue analysis is often necessary (and overlooked) to be sure the component works for repeated loading.
Tolerance Analysis
Tolerance stack analyses are the quintessential detail design phase responsibility of the design engineer. Verifying that complex features of a single part, or many features of many parts all work together is the definition of attention to detail. Hundredths of a millimeter, or less, can matter. Tolerance analyses are deeply integral to feature control through GD&T.
Drafting and GD&T
Again, pretty CAD models are great, but how do you manufacture, control, and accept the inevitable physical deviations from CAD?
Design for manufacture, quality, inspection, and design intent all come together in the component’s controlling document. That could be a traditional drawing or via Model Based Definition (3D), both are mediums I have experience with. The most explicit and complete way to do this is per geometric dimensioning and tolerancing as defined in ASME Y14.5, which is necessary for tolerance analysis.
Test Engineering
You’ve got a prototype in-hand, now what? A methodical approach to testing that precious prototype will yield the maximum information to be incorporated into the design.
While never explicitly a test engineer, I have advised and worked closely with Test Engineers while in aerospace and consumer products. At times I’ve needed to be my own test engineer, devising test plans, test methods, designing fixtures, and performing static and fatigue tests myself. The feedback loop for a design engineer isn’t complete until tests have been performed and the results are captured.
Document Control
All the previous activities and skills might yield a successful product. However, without a robust document control mindset and process, the information generated during the design phase won’t be sustainable for the lifecycle of the product. Document control closes the design process loop. The deliverable of Design, is not products, it is information how to create products.
In both small and large organizations I have driven improvement in Doc. Control or created systems from scratch. Regulatory requirements often prompt the need, as in aerospace and personal protective equipment. How the organization executes that requirement can have a significant effect on its adoption and usefulness for the future. Doc. Control is often an overlooked portion of the design process. This is understandable, how sexy is PDM/PLM compared to shiny CAD models?
Lean Product Development
How does the product development team create information as quickly and efficiently as possible? How aggressive a prototype(s) concept should the team design and test to gain valuable knowledge of the concept? Should the team spend four weeks implementing and testing a new feature request? How much money should we spend trying to fix a problem in the design? When is an expedite fee from a manufacturer worth it?
These questions are ones that Lean Product Development can help inform. The days of one or two old-timers using intuition or a WAG are over—or at least they should be. I’m not discounting the valuable experience they may bring, I’m pointing out lack of repeatability, extendability, and the inherent fragility of this approach. The concepts of Lean Manufacturing are well accepted as the best way to mass-produce parts. Lean Product Development (LPD) however is less widely known, but just as powerful an approach to apply to the design process. Any modern successful manufacturer implements some level of Lean Manufacturing, similarly design and development departments need to implement Lean Product Development. This topic complements my interest and experience in improving an organization’s process of designing and supporting product throughout its lifecycle.
One concept which I have kept closely in mind throughout my career is one from my undergraduate days, from my senior year project advisor, Robert Norton, PE. The quote below is at the beginning of one of his books, one which is in my top 5 reference materials. While this is only an excerpt of the section, The Design Process, I believe it is a good summary of my approach to engineering.
It ultimately does no good to have creative, original ideas if you do not, or cannot, carry out the execution of those ideas and “reduce them to practice.” To do this you must discipline yourself to suffer the nitty-gritty, nettlesome, tiresome details which are so necessary to the completion of any one phase of the creative design process.
R. L. Norton, Design of Machinery, 2nd Ed.
Pete Wilk Engineering, LLC
While the bulk of my career has been direct employment I created a freelance contracting and consulting company in 2016. Through my company I’ve had the opportunity to work on a variety of projects which offered more variety than just aerospace and consumer products. I will not claim expertise in electronics or medical implants, however I have worked on products in these areas and can bring the maturity of my engineering skills to these fields as well as others.
Please use the contact form to reach me to discuss how I might be involved in solving your engineering challenges.
Portfolio
If you’re interested in only seeing pretty pictures click here to go to those.
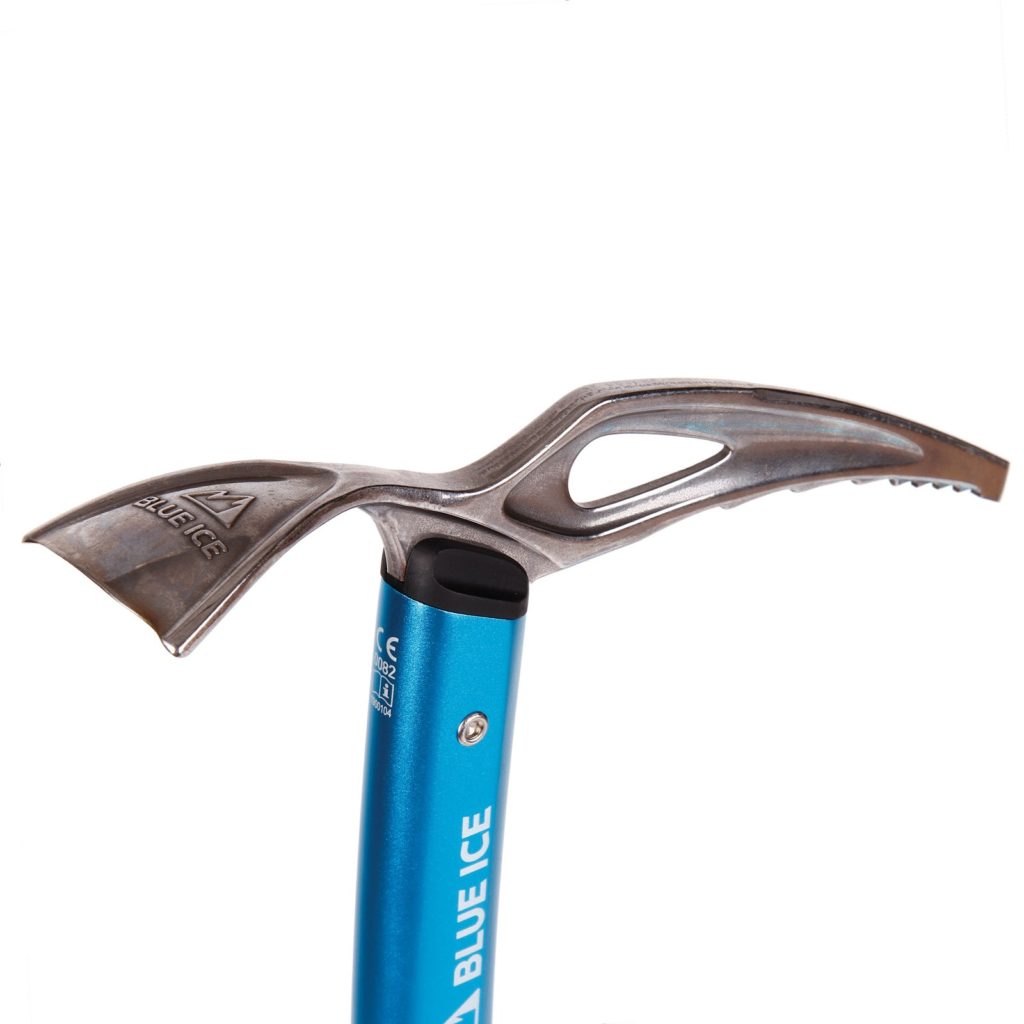
Complex surfacing can be quite deceiving when eventually produced, it can look obvious, simple, and elegant—which is the intent. However, the engineering work to get there can be complex. The Blue Ice Bluebird Ice Axe is one of my favorite products that I have worked on. It brought together much of my experience in surfacing, design for plastic injection molding, and simulation into one product.
Image ©Blue Ice
Another proud accomplishment of mine is the Blue Ice Aero Lite Ice Screw. It is a continuation of ice screw work that I did before. The design, while only three basic parts: tip, body, and hanger, required the integration of design for manufacture in order for it to be produced. Tight tolerances for the machining, deceptively complex surfacing for forging for the hanger, and numerous prototypes to test functionality and strength.
Image ©Blue Ice
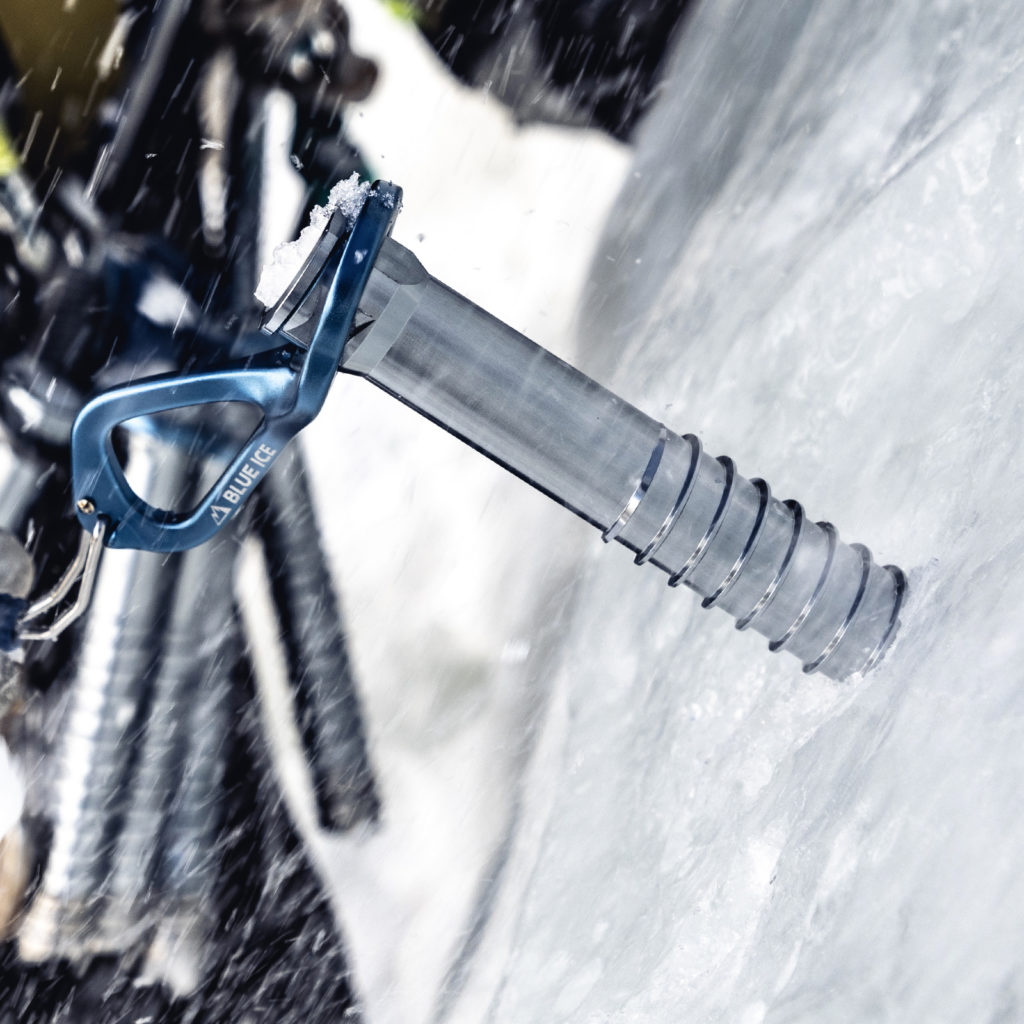
Below are a selection of products from Blue Ice that I worked on.
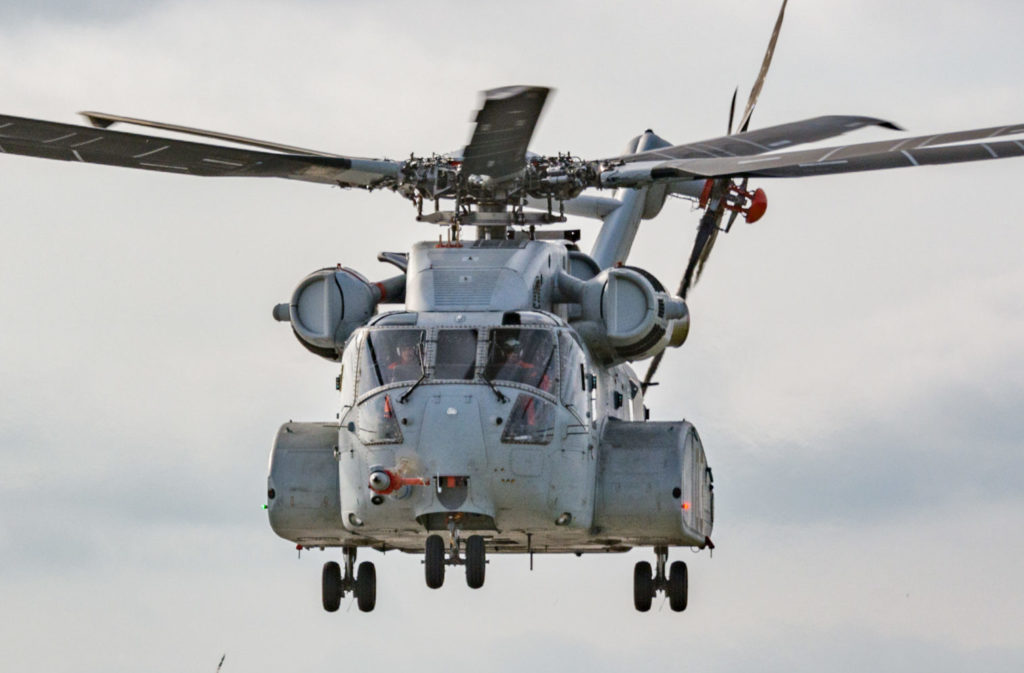
One of my proudest professional achievements is to have worked on the CH-53K helicopter while at Lockheed Martin Sikorsky. I had the responsibility to design and analyze the control system for the rotor head, seen in this image as the stuff between the hub & blades and the fuselage.
Image ©Lockheed Martin
Of course a product of this size, complexity, and scope means I was part of a team. Mentors, friends, and co-workers hammered in my knowledge of CAD, structural analysis, FEA, and many other skills to produce the largest capacity helicopter used by the US military. I would consider much of my formative professional experience to have developed working at Sikorsky.
Image ©Lockheed Martin
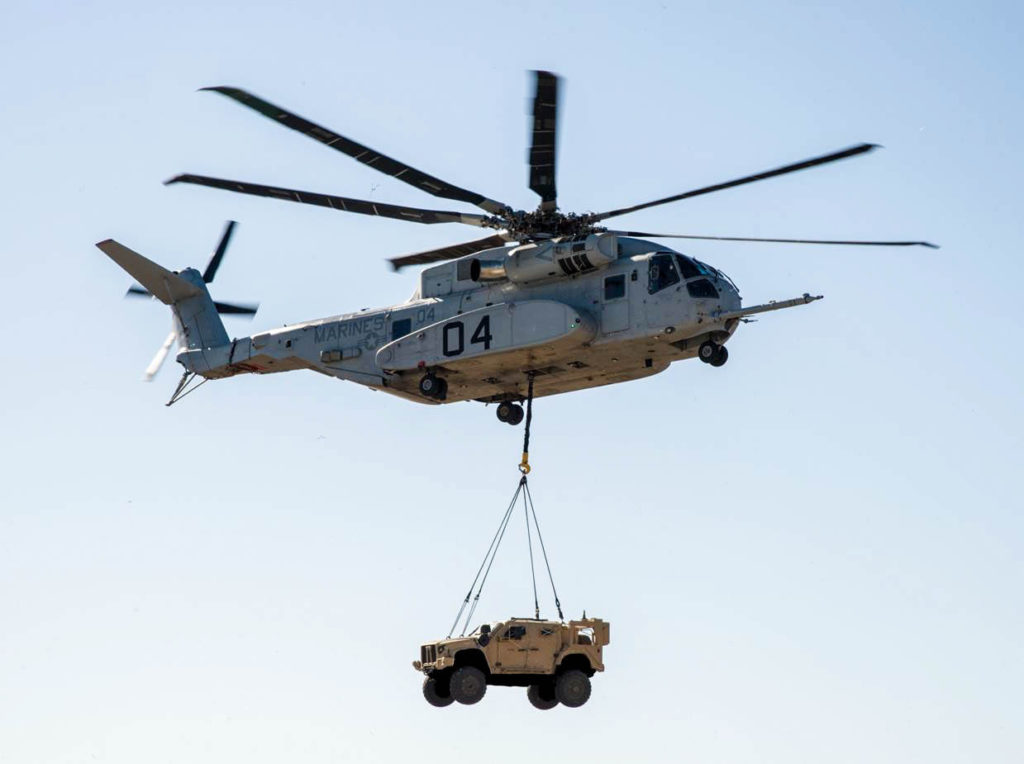
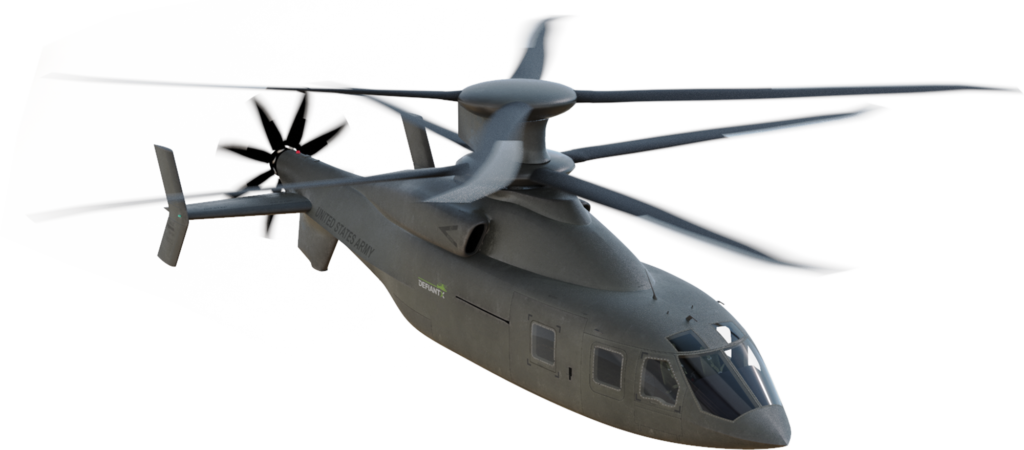
From 2020 thru 2021 as a contractor at Lockheed Martin Sikorsky, I had the pleasure to work on the next generation of rigid bladed, counter rotating rotors. I worked with a small team of new and experienced engineers on the rotor head and controls. During this project I was able to share some of my perspective from the consumer product world with the comparatively sluggish aerospace world. Along the way I was able to do some interesting fatigue and frequency response analyses.
Image ©Lockheed Martin
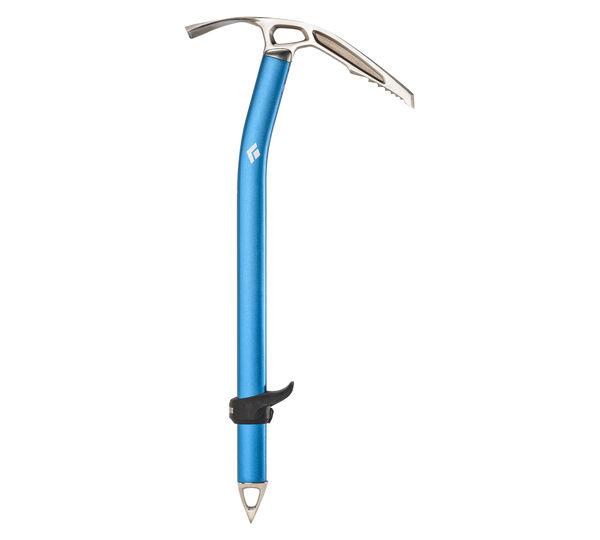
Consumer products are a very different animal than aerospace. Smooth curves, complex surfacing, cost, lead time, market need, are things that I learned working for Black Diamond Equipment. The transition from stogy aerospace industry to consumer was confusing and difficult at times. There are valuable aspects of both that I now bring to my perspective—attention to detail, robustness, sophisticated analysis from aerospace and nimbleness, flexibility, and wide-ranging materials and processing from consumer.
Image ©Black Diamond Equipment
My role at BD was the ice category designer. Much of my time was spent redesigning and improving the crampon and ice tool product line. This product, the Venom Ice Axe, took an outdated design and make the replaceable picks consistent across the entire BD range of ice axes. A dual shot handle required a lot of nuanced surfacing to maintain wall thicknesses and draft angles. The movable pommel (at right) allows on the fly adjustment without tools.
Image ©Black Diamond Equipment
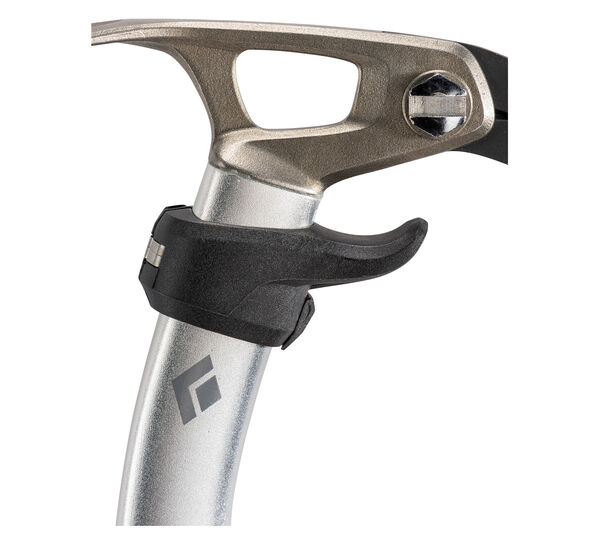
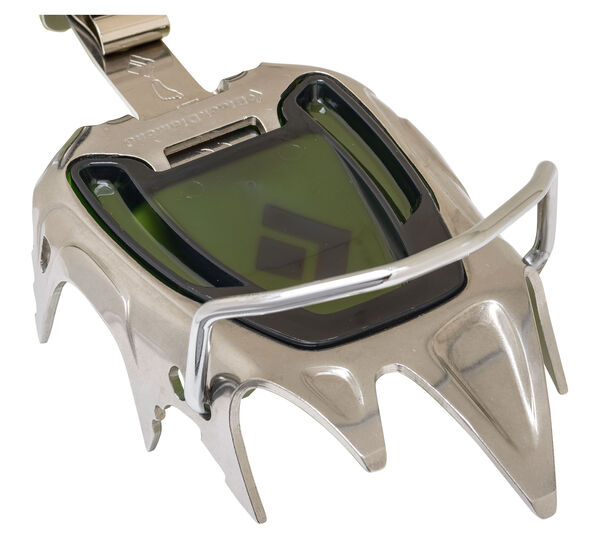
One of my standout projects is the Snaggletooth Crampon, a horizontal monopoint crampon. This product is one of the most versatile crampons available. Nearly every part of this product was new and I was solely responsible for the CAD and analysis for the product. At first glance it appears to be a sheet metal design, however closer inspection shows that it is a drawn part. Coining and complex bend lines all made this challenging to design.
Since prototyping this type of part is difficult considerable time was spent simulating the function of the crampon. Each tooth was checked under load to determine the minimum stress concentration possible.
Image ©Black Diamond Equipment
Concurrent to the Snaggletooth was also redesigning the Serac and Sabertooth crampons to improve their fatigue life. While this was not particularly difficult because of my fatigue skills from Sikorsky, the real accomplishment was to work closely with the manufacturing engineer to produce a flat pattern and die tool set that met the design intent first try—almost unheard of at the time for the company.
Image ©Black Diamond Equipment
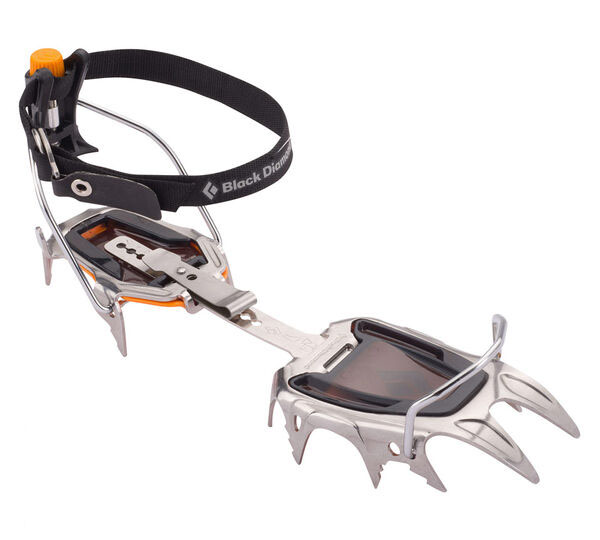
Below are a selection of products from Black Diamond that I worked on.
My contracting work has run across many industries, consumer products, medical devices and implants, to the agriculture industry. Here are a few.
Knee Implant Image ©TJO Inc; Platform photos ©Matt Oakley; Platform renderings ©Peter Wilk;